So I finally decided that I needed to go ahead and bite the bullet with the small rust bubbles that were showing up on my rocker panels (outer sills). I applied the angle grinder and here's what I found:
:dead:
So after that I decided the whole bottom was rotten and ended up with this:
What isn't shown is the curved end sections that are behind the fender in the front and quarter panel in the back are also "holey".
So, now my question is: does anyone manufacture a rocker patch panel? I guess I could cut out the whole face and weld in a new piece. The other side isn't so bad, only the curved end section at the back behind the quarter is shot:
Any ideas other than getting some flat metal and a brake? The rocker has a subtle curve to it that I think I would need a roller or english wheel to recreate. I don't have an issue with butt-welding sheet metal, but I do like to minimize the amount I have to do. I usually like to use my pneumatic puncher to set up some plug welds that replicate the factory spot welds and put a complete panel in. I know Matt has a couple of NOS complete rocker-door frame stampings for sale, but that seem like a bit of over-kill in this situation.
How have you guys fixed your rocker panels in the past?
Thanks,
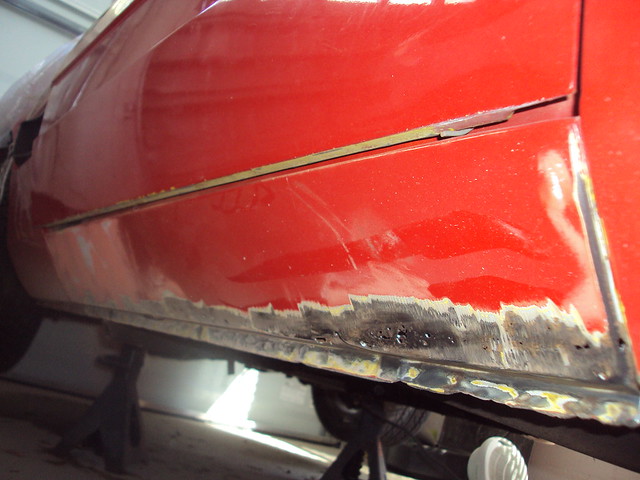
:dead:
So after that I decided the whole bottom was rotten and ended up with this:
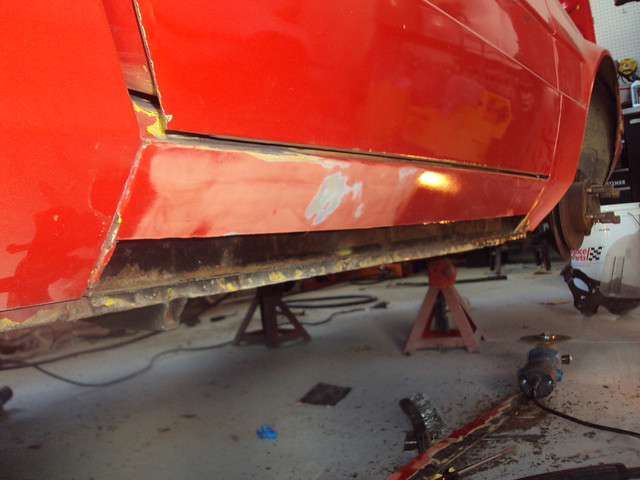
What isn't shown is the curved end sections that are behind the fender in the front and quarter panel in the back are also "holey".
So, now my question is: does anyone manufacture a rocker patch panel? I guess I could cut out the whole face and weld in a new piece. The other side isn't so bad, only the curved end section at the back behind the quarter is shot:
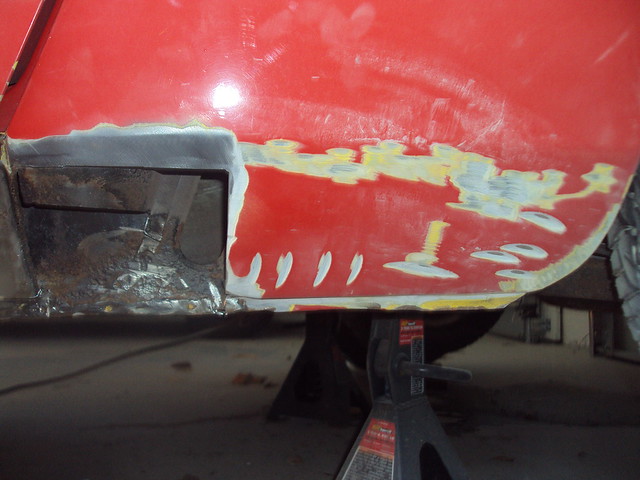
Any ideas other than getting some flat metal and a brake? The rocker has a subtle curve to it that I think I would need a roller or english wheel to recreate. I don't have an issue with butt-welding sheet metal, but I do like to minimize the amount I have to do. I usually like to use my pneumatic puncher to set up some plug welds that replicate the factory spot welds and put a complete panel in. I know Matt has a couple of NOS complete rocker-door frame stampings for sale, but that seem like a bit of over-kill in this situation.
How have you guys fixed your rocker panels in the past?
Thanks,
Last edited: